Анализ масла для обеспечения надежности промышленных предприятий
Введение
В данном разделе представлены три тематических исследования, которые доказывают, что программы анализа масла на месте эксплуатации оборудования промышленного предприятия дают выдающиеся результаты с точки зрения окупаемости инвестиций и сокращения сроков окупаемости. Эти программы помогают снизить расходы, особенно затраты на техническое обслуживание, что позволяет повысить прибыль.
Благодаря разработке на промышленных предприятиях программы смазки на основе анализа смазочных материалов вместо использования календарных графиков, результаты анализа масла становятся лучше, а восстановление масла — еще лучше. Эти программы гарантируют, что смазочные и гидравлические жидкости в процессе эксплуатации остаются чистыми, сухими и пригодными для использования в тех областях применения, в которых они работают.
Например, программа смазки на заводе по сборке автомобилей показала рентабельность инвестиций более 700% при сроке окупаемости 2 месяца. Другой пример: программа смазки на нефтеперерабатывающем заводе позволила сократить количество заказов на техническое обслуживание на одну треть, с 995 до 674 заказов на работы, связанные с отказами. Снижение затрат достигается в трех основных направлениях: сокращение потребления жидкости, сокращение случаев экстренного технического обслуживания и откладывание сроков технического обслуживания.
В большинстве промышленных областей применения масло не нагружается до такой степени, чтобы оно быстро разлагалось. Однако дизельные двигатели большой мощности, высокие температуры и агрессивные химические среды являются исключением. Задача в этих областях применения:
- Мониторинг/снижение загрязнения системы
- Контроль/снижение механического износа
В большинстве случаев знание того, когда и как правильно фильтровать масло, может вернуть его даже в более качественное состояние, чем у нового масла. Эта информация и последующие действия могут легко снизить потребление масла до малой доли от текущего уровня. В дополнение к этому значительно повышается надежность оборудования.
Следовательно, полная программа смазки оборудования промышленного предприятия должна включать следующие процессы:
- Анализ масла на месте эксплуатации для проверки всего нового масла
- Организованное хранение и распределение смазочных материалов
- Анализ масла на месте эксплуатации для определения состояния масла и результатов мониторинга
- Портативная автономная фильтрация для возврата масла в чистое состояние
Пример в целлюлозно-бумажной промышленности
Крупный целлюлозно-бумажный комбинат на юго-востоке Соединенных Штатов смог предотвратить выход из строя измельчителя древесины, который мог стоить компании целых 100 000 долларов из-за ремонта и потери производственного времени. Хрупкие баббитовые подшипники, направляющие вал измельчителя, рассыпались, возможно, из-за небольшого перекоса или дисбаланса, а начальник деревоперерабатывающего участка не знал об их состоянии. К счастью, недавно внедренная программа анализа масла на месте эксплуатации выявила проблему, что привело к предотвращению полного отказа.
Считалось, что смазка измельчителя была достаточной: проводилась ежеквартальная замена масла наряду с фильтрацией. Однако смазка по календарному графику часто не является удовлетворительным решением, особенно в грязных и пыльных условиях эксплуатации, где масло может очень быстро засоряться, создавая большие проблемы до наступления очередной запланированной замены. На многих целлюлозно-бумажные комбинатах обнаруживается, что смазка машин намного эффективнее и даже дешевле, если замена смазочного материала выполняется в зависимости от их состояния, которое можно определить с помощью программы периодического отбора проб и анализа масла.
Вместо увеличения стоимости обслуживания программа управления смазкой (включая отбор проб и анализ) может фактически сэкономить значительную сумму средств на большом комбинате, который может тратить 250 000 долларов в год или больше на смазочные материалы. Комбинат такого размера может разумно ожидать снижения расхода масла на 20% (50 000 долларов США) за счет замены масла в зависимости от его состояния, а не по календарю. Завод может увеличить сумму экономии более чем в три раза, т. е. 150 000 долларов в год, за счет сокращения ежегодных закупок, погрузочно-разгрузочных работ, хранения или утилизации 20% смазочных материалов.
Локальные лаборатории имеют смысл для большинства целлюлозно-бумажных комбинатов, которые обычно эксплуатируют более 100 систем смазки. Комбинат получает более качественный контроль над отбором проб, при этом анализ можно проводить сколь угодно часто. Результаты доступны немедленно, поэтому при необходимости можно очень быстро провести повторный анализ.
Майк Лоусон с целлюлозно-бумажного комбината Bowater в Калхауне, штат Теннесси, предпочел бы анализировать масло в редукторе по цене 15 долларов за пробу, чем проводить замену по 35 галлонов, общая стоимость которой составляет 480 долларов. Эта сумма включает 140 долларов за масло, 240 долларов за двух механиков, работающих в течение шести часов, 50 долларов за утилизацию отработанного масла и еще 50 долларов на пополнение запасов. Рентабельность инвестиций в этом случае составит 480 долларов США / 15 долларов США, что эквивалентно 3200 процентам!
На целлюлозно-бумажном комбинате была установлена система Spectro 5200 Trivector Minilab для проведения отбора проб и анализа масла, чтобы принимать решение о его замене. Результаты анализа подтвердили, что масло не разложилось и было довольно чистым. Замена этого масла не требовалась и могла привести к нежелательному загрязнению.
На следующем графике видно, что локальная минилаборатория, такая как Spectro 5200 Trivector Minilab, столь же эффективна, как и более дорогие независимые лаборатории, но при этом она демонстрирует более низкую стоимость каждой пробы и обеспечивает лучший возврат инвестиций (ROI), как показано на рисунке 15-1.
В заключение можно сказать, что на любом целлюлозно-бумажном комбинате, который отбирает и анализирует менее 50 проб масла в месяц, отсутствуют проблемы, которые требуют гораздо больших трудозатрат (и иных расходов) по сравнению с затратами на более обширную программу. Отбор и анализ 100 проб критически важного оборудования занимает около одной недели в месяц. Окупаемость труда и экономия намного выше, чем время, затрачиваемое на эту работу.
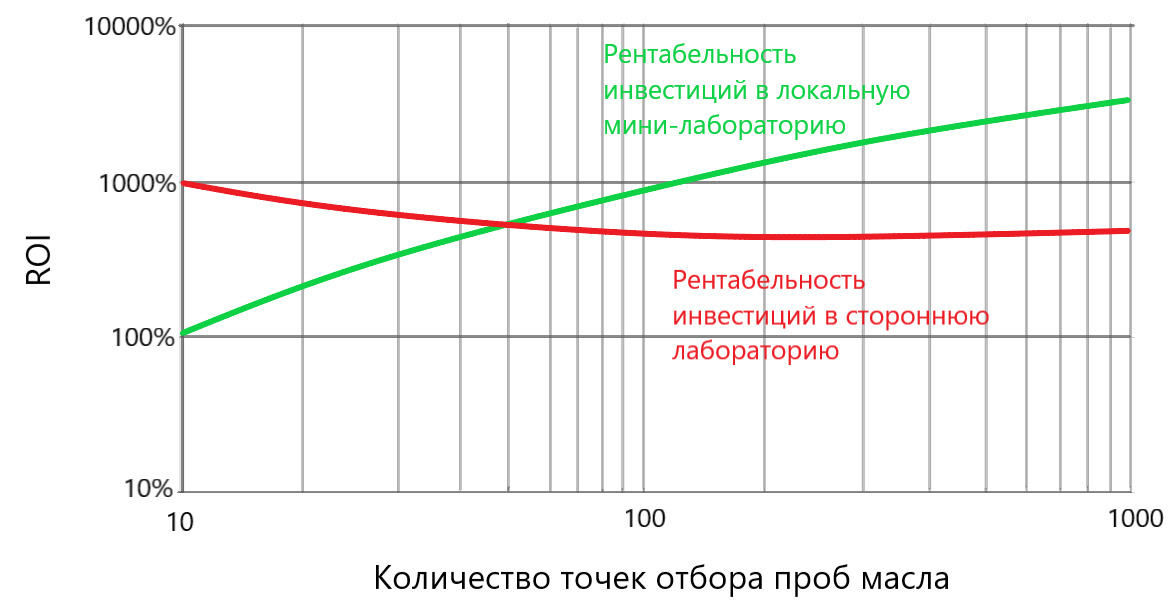
На целлюлозно-бумажном комбинате была установлена система Spectro 5200 Trivector Minilab для проведения отбора проб и анализа масла, чтобы принимать решение о его замене. Результаты анализа подтвердили, что масло не разложилось и было довольно чистым. Замена этого масла не требовалась и могла привести к нежелательному загрязнению.
На следующем графике видно, что локальная минилаборатория, такая как Spectro 5200 Trivector Minilab, столь же эффективна, как и более дорогие независимые лаборатории, но при этом она демонстрирует более низкую стоимость каждой пробы и обеспечивает лучший возврат инвестиций (ROI), как показано на рисунке 15-1.
В заключение можно сказать, что на любом целлюлозно-бумажном комбинате, который отбирает и анализирует менее 50 проб масла в месяц, отсутствуют проблемы, которые требуют гораздо больших трудозатрат (и иных расходов) по сравнению с затратами на более обширную программу. Отбор и анализ 100 проб критически важного оборудования занимает около одной недели в месяц. Окупаемость труда и экономия намного выше, чем время, затрачиваемое на эту работу.
Пример с тепловой электростанцией
Подобно целлюлозно-бумажному комбинату Bowater, электростанции могут получить большую выгоду от программ анализа смазочных материалов на месте эксплуатации. Например, тепловая электростанция Горгас на реке Уорриор недалеко от Бирмингема, штат Алабама, решила самостоятельно контролировать состояние масла, чтобы избежать особо опасных событий, которые могут произойти в случае выхода из строя одного из редукторов.
Поскольку большинство агрегатов станции построено в 50-х, 60-х и 70-х годах, загрязнение смазочного материала является большой проблемой.
Хорошая программа смазки, включающая анализ масла на месте эксплуатации, позволяет отслеживать тенденции состояния оборудования.
Эта возможность позволяет при необходимости оперативно реагировать на возникающие ситуации и потенциально может привести к значительной экономии. В сочетании с другими технологиями такой подход может обеспечить оптимальную работу электростанции.
С этой целью на станции теперь применяется анализатор масла Spectro 5200 Trivector. Входящий в его состав микроскоп позволяет проверять наличие продуктов износа, что крайне важно для нужд станции.
Проблемы начались во время планового ежемесячного анализа масла. Показания по ферромагнитным частицам ежедневно поднимались с нуля до 352–443. Анализ за предыдущий месяц показал нулевое содержание ферромагнитных частиц, что свидетельствует о возникновении проблемы. После слива жидкости из редуктора и осмотра внутренних деталей было обнаружено, что упорный подшипник изношен до такой степени, что отказ редуктора неизбежен. К тому же форсунка 10-B не дожила бы до периода максимальной нагрузки.
Подшипник был оперативно заменен, через два месяца после первоначального обнаружения содержания ферромагнитных частиц вопрос был исчерпан. Повторная проба масла показала полное отсутствие ферромагнитных частиц.
Выясним, как достигается еще большая экономия. Когда компания Alabama Power столкнулась с подобной проблемой, еще до того, как она начала использовать локальную лабораторию, полный отказ редуктора потребовал капитального ремонта, стоимость которого составила более 400 000 долларов. Однако, благодаря возможности предотвратить этот отказ с помощью анализа на месте эксплуатации, общие затраты составили всего 20 000–30 000 долларов на подшипник и 10 000 долларов на установку.
Пример на заводе Rominserv
Rominserv — румынская компания, которая специализируется на промышленных услугах, техническом обслуживании, управлении проектами и технической модернизации. Компания содержит лабораторию профилактического обслуживания, в которой проводится обработка и оценка данных о вибрации и масле, позволяя предсказывать, когда машине потребуется техническое обслуживание для поддержания ожидаемого уровня производительности.
Производя всего 10 500 тонн продукции в сутки, компания поставила перед собой цель выйти на полную мощность к 2009 году. В дополнение к увеличению производства компании требовалось сократить количество ненужных заказов на техническое обслуживание и снизить затраты. Кроме того, требовалось повысить общее качество, чтобы соответствовать мировым стандартам экспортного регулирования и увеличить общую эффективность оборудования (OEE).
Когда в компании Rominserv было решено внедрить программу профилактического обслуживания, основанную на мониторинге состояния, был выбран анализатор Emerson CSI 2130 Machinery Health™, взаимодействующий с приложением AMS™ Suite: Machinery Health Manager для поддержки этой программы. Чтобы получить полную картину состояния механического оборудования, компания Rominserv использовала анализатор масла Spectro 5200 Trivector Machinery Health Oil Analyzer для проверки качества масла и продления срока службы контролируемого оборудования.
Основные этапы программы
- Январь 2005 г. — первый сбор данных о вибрации с помощью CSI 2130
- Сентябрь 2005 г. — первый анализ смазочного масла с помощью анализатора Spectro 5200 Trivector.
- К февралю 2006 года база данных для платформы Petromedia (учредитель компании Rominserv) содержала около 1000 единиц вращающегося оборудования;
- В настоящее время с помощью AMS Machinery Manager контролируется более 1200 динамических единиц оборудования (электродвигатели, насосы, редукторы, вентиляторы, паровые турбины, центробежные и поршневые компрессоры).
Пример компании Rominserv № 1 — Результаты анализа вибрации
Периодически отбирая пробы масла в 150 критически важных машинах и анализируя их с помощью прибора Spectro Q5200 Trivector, можно выявить другие факторы, помимо вибрации, которые могут ухудшить характеристики вращающегося рабочего оборудования. Грязь и продукты износа, вода в масле и другие виды загрязнения приводят к раннему распознаванию возможных внутренних повреждений.
В этом случае благодаря анализу масла компания Rominserv избежала полного отключения установки, обнаружив серьезную проблему со смазкой в критически важной машине. По оценкам, экономия составила 7,3 миллиона долларов США.
Используя прибор Spectro Q5200 Trivector, компания сначала анализировала только вязкость масла. На представленных ниже графиках кинематическая вязкость составляет 27 сСт при 40 °C, а процентное изменение KV на уровне срабатывания аварийной сигнализации находится между синим и желтым цветовым кодом.
Третий анализ с добавлением центробежного действия с кинематической вязкостью 20 сСт при 40 °C дал процентное изменение при максимально допустимых уровнях (лиловый цветовой код). Кроме того, количество воды и частиц было в пределах нормы.
Анализируя данные диагностики, компания смогла определить как критические проблемы с оборудованием, так и проблемы, связанные с технологическим процессом оборудования. С помощью мониторинга вибрации компания смогла определить тип неисправности и точное место повреждения.
Так было при обнаружении преждевременной поломки предохранительного болта на роторе критически важного насоса. Неисправность могла привести к внезапной поломке насоса, в результате чего остановилась бы вся установка. Однако проблема была вовремя обнаружена, и поток без происшествий переключили на другой насос. Неисправный насос был демонтирован и отремонтирован без значительных повреждений. Ориентировочная стоимость производственных потерь из-за незапланированной остановки этого блока составила бы не менее 2,8 миллиона долларов США.
Пример компании Rominserv № 2 — Результаты анализа масла
......................................................................
===========
Кроме того, количество ремонтов уменьшилось за счет следующих факторов:
- Успешное применение программ профилактического обслуживания с использованием новых технологий
- Повышение качества ремонта и запчастей
- Осведомленность сотрудников о важности проведения качественного технического обслуживания
Компания Rominserv добилась следующих показателей:
- Сэкономлено около 10,1 млн долларов за счет исключения ненужных простоев
- Возврат инвестиций более чем в 10-кратном размере
- С 35% до 45% сократилось время простоя ремонтируемого оборудования
- Возможно увеличение производственных мощностей с 20%до 25% к 2009 г.
- Экономия от 25% до 30% на расходах на оборудование
Заключение
Как показывают конкретные примеры, промышленные предприятия могут получить значительную выгоду, имея хорошую программу анализа масла на месте эксплуатации с техническим обслуживанием по состоянию масла. Такая программа будет контролировать поставки масла, чтобы гарантировать, что масло чистое, сухое и пригодное для использования. Кроме того, сам по себе анализ продуктов износа указывает на то, что в оборудовании имеется повреждение поверхности. Заблаговременное знание этих показателей — гарантия того, что промышленное предприятие будет эксплуатировать качественное масло — ваш самый ценный товар.
Справочные материалы
Материал этой главы частично взят из следующих источников:
- C.C.IIie, Rominserv, Бухарест, Румыния, www.rominserv.com
- Рэй Гарви, Emerson Process Management, "Предотвращение простоев завода благодаря знанию состояния смазочных материалов"
- Рэй Гарви, Emerson Process Management, "Превосходная окупаемость инвестиций при поддержке программ смазки на промышленных предприятиях международными стандартами"
Нужен ли мне анализ масла в герметичной системе? Краткий ответ: да. Жидкости в этих системах по-прежнему должны циркулировать по системе и сжиматься с помощью насосов и спиралей.
Масло во вращающихся двигателях внутреннего сгорания постепенно загрязняется, скорость загрязнения может варьироваться в зависимости от коэффициента нагрузки, рабочего цикла, возраста, окружающей среды и типов топлива.